Полиуретановая форма своими руками в домашних условиях
Или как сделать форму из жидкого полиуретана самостоятельно
Не секрет, что в современном строительстве широко используются полиуретановые формы. Делается это в силу удобства применения данных матриц при производстве искусственного камня, строительных блоков, а также декоративного камня. Полиуретановые формы зарекомендовали себя как качественное подспорье в любом строительном вопросе. Однако, полиуретановая форма – это не инструмент исключительно профессионального строительства. Полиуретановые матрицы и формы для камня, например, широко применяются в быту. Конечно, можно купить полиуретановую форму. Однако будет ли такая матрица в полной мере соответствовать вашим требованиям и ожиданиям.
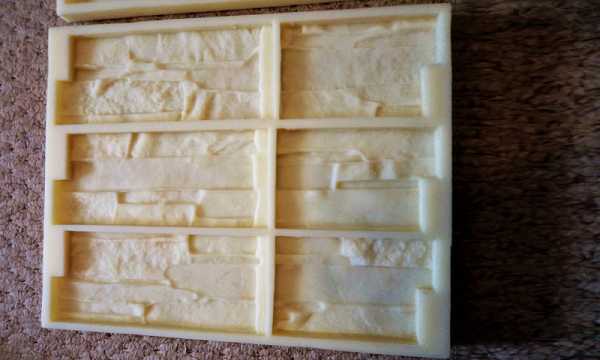
Мы же предлагаем следующее: изготовить полиуретановую форму своими руками. Во первых, данное мероприятие выйдет вам намного дешевле, чем покупка готовой формы для камня – по нашим подсчётам, стандартного полиуретана для форм на 10 кг, фасованного в комплекты, в среднем хватает на 2 больших и 1 маленькую форму. Это при том, что по цене данный комплект будет стоить немногим дороже чем готовая форма. И во вторых, полиуретановая форма сделанная своими руками будет чистой воды эксклюзивом, который вы изготовите исключительно под свои нужды и потребности.
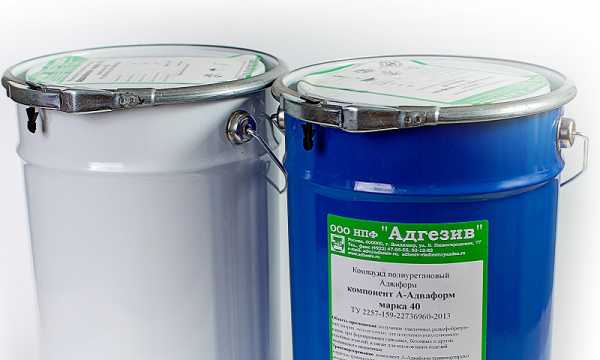
Производство полиуретановых форм в домашних условиях
Как мы писали выше, многие частные мастера имеют заблуждение на счёт гибких матриц для камня, а именно — они думают, что полиуретановая форма – это не инструмент, который можно изготовить самостоятельно. Спешим вас разуверить в этом. Такие матрицы изготавливаются намного легче, чем вы себе представляли раньше. В связи с этим, ниже мы размещаем пошаговую инструкцию, в которой с удовольствием опишем, как изготовить полиуретановую форму своими руками в домашних условиях.
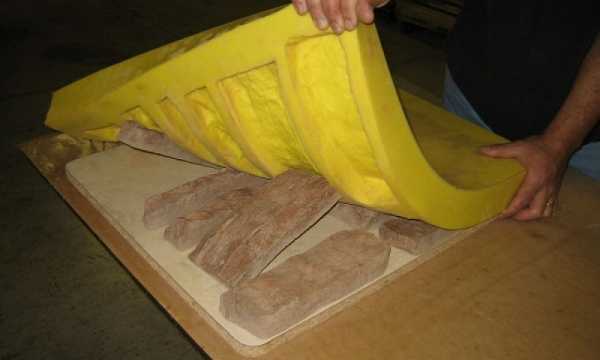
Подготовка мастер модели для литья форм
В первую очередь вам будет необходимо найти, приобрести или изготовить самостоятельно необходимые образцы камня, которые планируется копировать в полиуретановой форме. Данные образцы в нашем случае называются мастер моделями, и к ним имеется ряд некоторых требований:- 1. Задняя, не рельефная часть камня должна быть абсолютно ровной.
- 2. Фронтальная часть камня должна иметь ярко выраженный рельеф, который мы хотим запечатлеть в полиуретановой форме.
- 3. Камень не должен иметь зазоров, швов, трещин, отверстий и прочих деформаций, которые помешают литью полиуретана или приклейке мастер модели к поверхности.
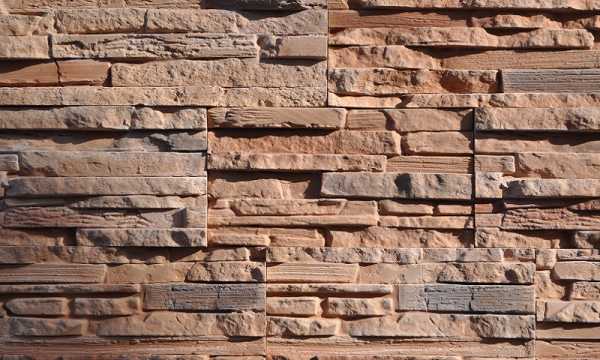
Изготовление полиуретановой формы на этапе опалубки
Заготовленные мастер модели камней необходимо плотно приклеить к какой либо поверхности, которая будет заливаться жидким полиуретаном. В качестве этой основы может выступать стол, лист ДСП, обычная деревянная доска оптимального размера или прочее. Каменные образцы сажаются на эту поверхность на клей или иной герметик, после чего вам необходимо дать время для его высыхания. После того, как наши камни надёжно закреплены на поверхности – обрезайте лишние края основы и делайте борты, так как сделали бы их для опалубки. Борты также можно прикрепить к основе с помощью герметика или клея. Следите за тем, чтобы в опалубке не было щелей и трещин.

Литье полиуретана для форм под изготовление гибкой матрицы
Когда все приготовления закончены, перво — наперво не забудьте обработать мастер модели и внутренние поверхности опалубки смазками, которые предотвратят прилипание полиуретановой формы.
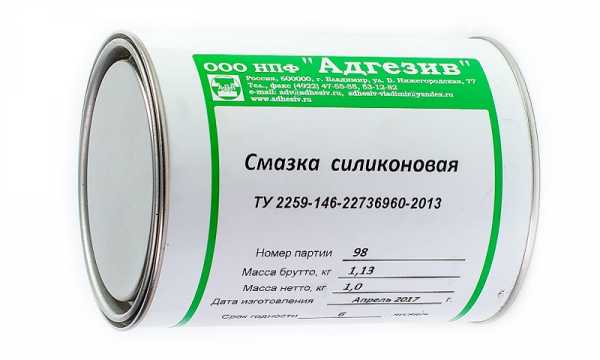
И вот, наконец, можно приступать к литью. В данной инструкции материалом для литья у нас выступает полиуретан для форм холодного отвержения. Исходя из этого, будем равняться на этот материал в описаниях. Готовим литьевую смесь из компонентов полиуретана так, как это указано в инструкции.
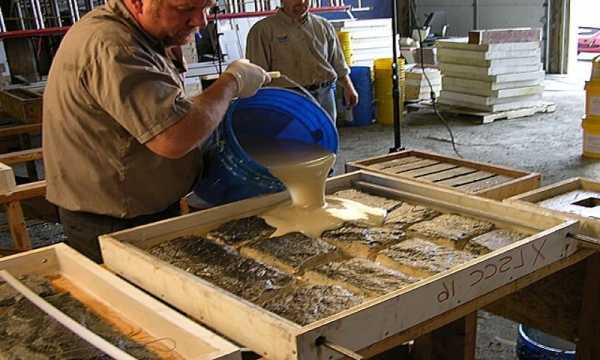
Например, жидкий полиуретан для форм Адваформ, является очень текучим материалом, поэтому не требует дополнительной дегазации, но если вы работаете не с Адваформом, то после смешивания, жидкий полиуретан необходимо дегазировать. Сделать это можно в вакуумной камере или на вибростоле.

Когда с данным этапом покончено, можно приступать к литью нашего полиуретана. Аккуратно заливаем смесь в опалубку так, чтобы камни скрылись под слоем материала и оставляем полиуретан затвердевать.
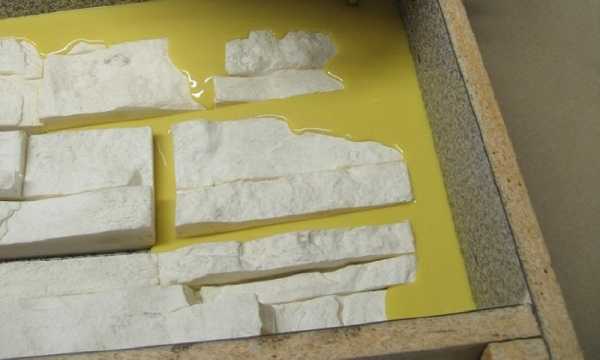
Спустя сутки форму можно будет изымать из опалубки.
Вот и вся несложная наука о том, как правильно изготовить полиуретановую форму своими руками. Вдохновения вам, мастера.
kremen.ru
Как сделать полиуретан
Синтетическое вещество под названием «полиуретан» используется во многих сферах человеческой жизни благодаря своей эластичности и некоторым другим достоинствам. Медицина, строительство, одежная и обувная промышленность – с успехом применяют его в свой деятельности.
Также приобретает популярность полиуретан со смоляной консистенцией — ХанзаКрил Эластик Гидропротект — для разрешения сложных ситуаций, с которыми другим изоляторам справиться проблематично.
Характеристики материала
Давайте рассмотрим основные важные характеристики полиуретана:
- долгий срок эксплуатации;
- выдерживает различные температуры;
- стойкий ко внешнему воздействию, а также старению и износу;
- прочный и надежный;
- может использоваться при действии большого веса;
- служит материалом для изготовления многих вещей ежедневного обихода;
- демократичная стоимость, позволяющая использовать его многим слоям населения;
- удобный в использовании и многозадачный;
- не изменяет форму под физическим воздействием;
- после взаимодействия его с различными поверхностями отсутствуют следы;
- способен функционировать в агрессивной среде и при различных природных условиях.
На эластичность полиуретана можно влиять во время его производства.
Особенности получения
Процесс изготовления полиуретана является трудоемким. На дорогом оборудовании подвергаются тепловой обработке и смешиваются такие составляющие:
- полиол;
- изоциант;
- полиэфирамины.
Материал изготавливают литьем, прессованием, экструзией. Сырье для него можно найти лишь в некоторых странах: России, Италии, США и Германии.
Используется для обеспечения людей шинами, матрасами, утеплителями, сумками, обувью, элементами отделки (карнизами, потолочными плинтусами, лепниной) и многими другими необходимыми вещами.
Использование жидкого полиуретана
Это синтетическое вещество применяется в различных физических состояниях:
- жидком;
- твердом;
- в виде пены.
Жидкую разновидность этого материала можно увидеть в кровельном деле, потому как стойкость к влаге и износу помогает качественно ликвидировать зазоры в покрытии.
Преимуществами использования являются:
- доступность;
- надежность;
- легкость в работе с ним;
- экологичность;
- не подверженность действию окружающей среды;
- на высыхание требуется немного времени.
С помощью такого материала осуществляется качественная и долговечная гидроизоляция.
Смотрите также:
![]()
Как выбрать насосы для воды http://euroelectrica.ru/kak-vyibrat-nasosyi-dlya-vodyi/.
Интересное по теме: Тиристоры в помощь электрику
Советы в статье «Как подключить оптоволокно » здесь.
Литьевой полиуретан: что это и как с ним работать:
Делаю полиуретан! — бортжурнал BMW 7 series 730. Красивая зараза! 1993 года на DRIVE2
В общем главное уже в теме написано. Ибо проще сменить сайлентблоки на полиуретановые, чем сменить дороги…
Пришёл я к этому просто — стало «плющить» и «выворачивать» нижние сайлентблоки на задних амортизаторах. Долго не мог понять причину, но потом выяснили — были погнутые задние рычаги, которые конечно же отремонтировали и историю об этом можно прочитать здесь: Ремонт задних рычагов — или не пытайтесь бороться с жёром задней резины «не теми» способами!
Какие только варианты замены мне не советовали, но я решил твёрдо и бесповоротно — сделаю полиуретановые сайлентблоки. Пошёл к батиному товарищу с вопросом: — Кто и где льёт? Оказалось — у него в гараже стоит шприц-пресс, на котором и отливали разные вещи в своё время…
Но лить сайлентблоки из термо-экструзионного полиуретана — это дело дорогое. Ибо под любой сайлентблок автоматически необходима своя литьевая форма! Стоимостью от 500 у.е. до 5 килобаксов в зависимости от сложности…
Но всегда есть и простой выход! И мы его нашли. Лить стержни, потом из них точить сайлентблоки и запрессовывать.
Звоню токарю моему. Заказываю форму под стержень, спустя несколько дней забираю форму, отливаем стержень, точим, запрессовываем и…
… смотрим результаты работы по замене мне самому:
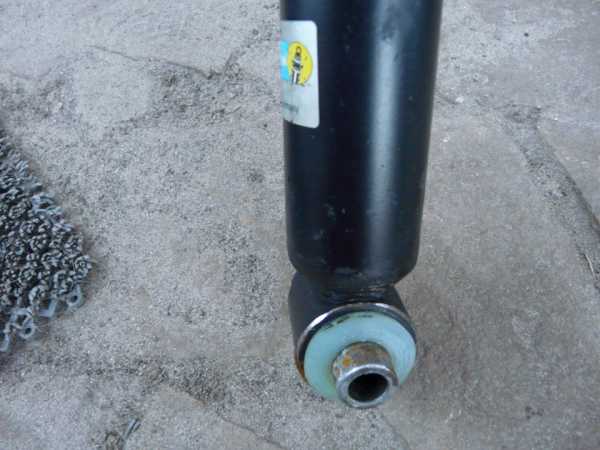
Мой Бильштайн.
Когда на них (с их-то собственной жёсткостью) ещё и поставил полиуретановый сайлентблок и усиленные верхние опоры задних аммортизаторов, задок машины стало не узнать! Это просто другая машина стала!
Контролируемая, прогнозируемая, внятная, и очень-очень собранная! Без непонятных виляний, плаваний, и прочих раздражающих водителей БэМэВэ неприятностей!
Ещё примеры работ некоторым знакомым:

Товарища Заксы

Тоже товарища — вид в профиль
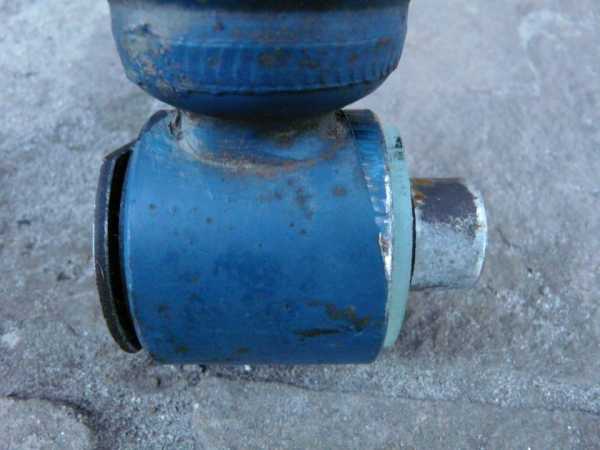
Мои Мейле со второй машины
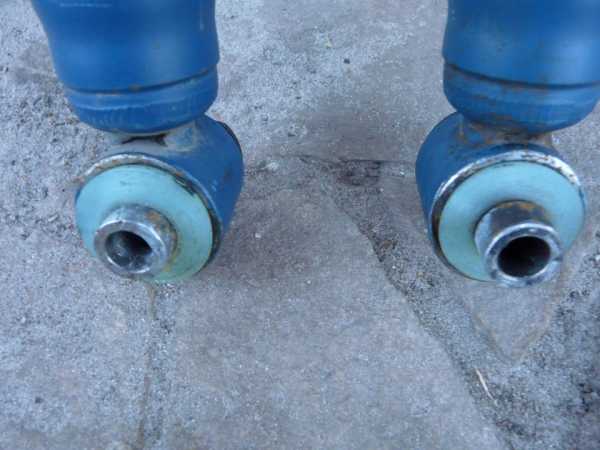
Мейле анфас.
Но дальше — больше! Попались мне в продаже сайленты скажем так «конкурентов»:
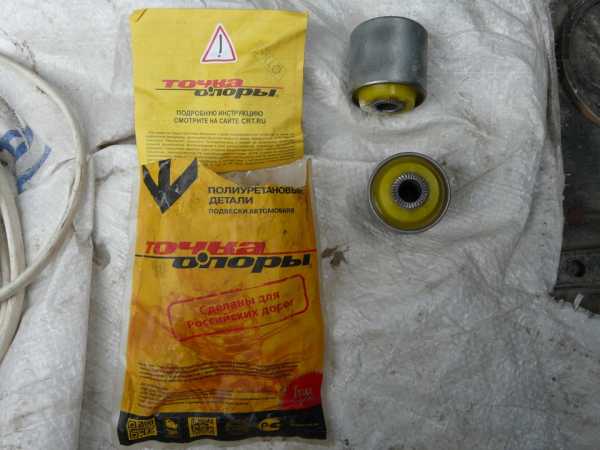
Фирма производитель — »Точка опоры». Делают дорогие Россияне. Во Владике где-то.

Решил купить, попробовать, чем конкуренты дышат… =)
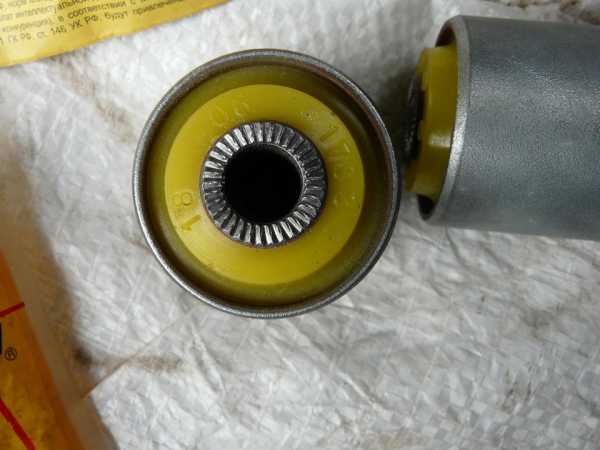
Они ставятся в нижние рычаги, которые сами по себе в общем-то не сильно проблемные. Родные сайлентблоки там служат годами.
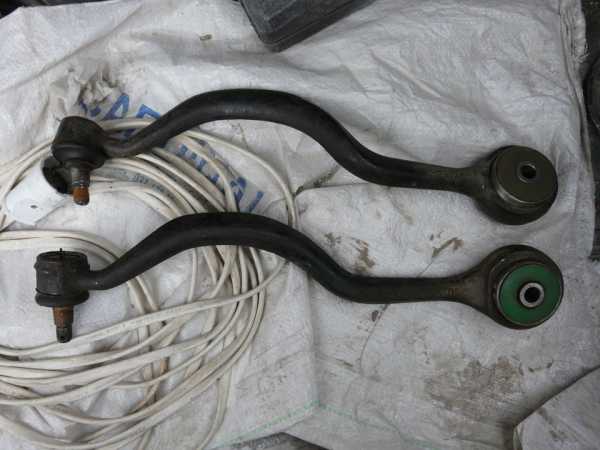
А вот это уже мои рычаги с моим собственным полиуретаном. Решил для разнообразия сделать зелёненькие. Типа — зелёная дорога!
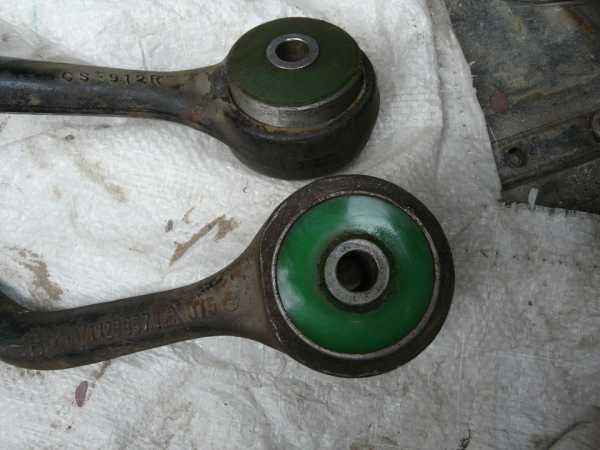
И вот именно на верхние рычаги сайлентблоки с нашими дорогами для меня стали настоящим проклятием! Я попросту заколебался их менять. А ведь кроме покупки часто платишь за работу дяде, когда нет сил или времени сделать самому! Ставил стандартные. Ставил усиленные, которые шли не с синей пластмасской, а с зелёной (это которые ставились только на 750 и 750 лонг). И каких фирм я только не пробовал покупать! Единственное, что я не покупал — это оригинал. В силу высокой стоимости. И усиленные, которые шли на бронированные семёрки. Но они тоже выпускаются только в оригинале и стоят вообще космических денег! А того, что из не оригинала ставил, хватало от пол месяца до пол года. Почти не помню сайлентблоков, которые бы проходили год! Хотя и езжу, если честно, не разбирая дорог… :=)
Первые впечатления от езды: — Куда, мля, подевались рельсы, которые я каждый день переезжаю поперёк по нескольку раз на день выезжая с моей улицы? Ну ничего не гупает, не грюкает!
Второе впечатление от езды на них — Нереально приятное торможение! Это просто пипец, насколько машина стала цельна с тормозами и колёсами!
Клевки свелись к минимуму! Ощущение от торможения сходно с тем, что испытываешь сидя в поездах-экспрессах — поступательное и неотвратимо уверенное замедление!
Дальше только удивлялся изменившейся управляемости и общему ходу авто на неровностях! Осоообенно типа — «тёщин язык»… Там, где все уже ударили по тормозам и начали исчезать в зеркале заднего вида, я продолжаю ВААААЛИИИИТЬ! И это радует!
И уже сразу же через месяц-полтора эксплуатации вылезли проблемы с продукцией «конкурентов»! Сайлентблоки этой фирмы слишком мягкие… При диагностике новых звуков в ходовке (возникших из-за износа подшипника передней левой ступицы) дёргали и рычаги. По нижним люфт и большой! Причина — они мягкие настолько, что на нижних рычагах это перебор.
Итоги и выводы об эксплуатации почти полного набора всего из полиуретана в ходовой часто авто:
1. Тот полиуретан, который я себе лил на задние амортизаторы, имеет максимальную жёсткость по Шору — 95 единиц. Честно — жестковато. Можно было как на передок сделать.
Можно делать и 95, но для машин, которые либо на треках гоняют, но при этом эксплуатируются и как уличные авто и не желают расставаться с комфортом на все 100%, либо для тачек, которые мотаются только по трассе.
2. То, что отлил и поставил на передние сайленты — 85 единиц. Самое то! Город + большой вес авто + 85-я жесткость = идеальное соотношение.
3. То, что сделали конкуренты, нажимается пальцем и продавливается легко так, что мне кажется там не то, что 85 единиц нету, вопрос — есть ли там 75?! Скорее всего — даже ниже. В общем экономят на сырье конкуренты. Буду менять их сайлентблоки на свои при ближайшей смене рычагов (то есть теперь что раньше умрёт — либо шаровая, либо сайлентблоки конкурентов). Вывод — не конкуренты они мне!
Можно конечно ставить и такие сайлентблоки, как у них. Только на машинки весом до тонны. Тойота Корола, Дачя Логан, Хёндэ Солярис там, Киа Рио, ТАЗы… Ну вы поняли.
Ну, и кто заинтересовался — обращайтесь в личку. Отправка по Украине почтовыми службами. Цены более, чем гуманные!
А сегодня, по такой цене, не все могут сделать. Вернее сделать могут не только лишь все, мало кто может это делать. =)
www.drive2.ru
Полиуретан своими руками (видео) | CassusPro.ru
(Last Updated On: 04.03.2018)Полиуретан своими руками
При использовании в дизайне интерьера определенного стиля нужно обязательно проследить за тем, чтобы все детали, каждая мелочь соответствовала выбранному стилевому направлению. И даже не только использование чуждых элементов, но и просто пустое место может разрушать целостность восприятия, например, незакрытые стыки потолка и стен из-за своей убогой прямоугольной формы никак не вписываются в роскошные интерьеры барокко или ампира. Такие стыки рекомендуется закрывать специальной лепниной, не обязательно гипсовой, вполне применима полиуретановые изделия, они и стоят дешевле, и весят меньше, да и обрабатывать и клеить полиуретан своими руками куда проще, чем тяжелый и хрупкий гипс.
Торжество технологий и прогресса
Полиуретан – это синтетический материал, получивший сегодня настолько широкое распространение в строительстве, что он уже воспринимается как органичный и даже обязательный элемент любого дома. Производство и применение полиуретана было внедрено в 40-х годах двадцатого века в Германии. В послевоенное время технологии создания и применения распространились на всю остальную Европу. Основное его предназначение в ту пору, как, впрочем, и сегодня – это проведение изоляционных работ. Практически сразу после начала его массового использования полиуретан стал вытеснять натуральные изоляционные материалы – каучук, пробковое дерево и другие. За счет своей легкости и минимальной теплопроводности он мог использоваться практически в любых условиях. А продолжавшиеся исследования позволили улучшить его потребительские качества и значительно расширить сферу его применения. Сегодня полиуретан своими руками используют, вероятно, все строители и отделочники, наиболее распространенная форма использования – это монтажная пена, в которой полиуретан является одним из основных компонентов.
Видео:
Декор из полиуретана – просто, удобно, качественно
Вернемся все-таки к полиуретановой лепнине и особенностям ее монтажа. Скажем сразу, что мы не будем рассматривать вопрос, как произвести полиуретан своими руками – это процесс, связанный со сложными химическими элементами и реакциями, поэтому изготовить полиуретан в домашних условиях практически невозможно. Поэтому лепнину все-таки придется купить. Продается она либо поштучно, если это отдельный элемент декора, либо по метражу, как, например, карнизы и потолочные плинтусы. При покупке последних лучше взять с запасом на тот случай, если где-то Вы ошибетесь и неправильно отрежете, возьмете неверный угол и т.д. Если элементы имеют сложный орнамент, то нужно рассчитывать необходимое количество материала таким образом, чтобы орнамент на разных сегментах хорошо стыковался.
Пилить полиуретан своими руками проще всего ножовкой с мелким зубом, она позволит выполнить распил качественно и не сохранит поверхность распила ровной. При распиливании нужно прочно зафиксировать элементы, чтобы исключить биение и искривление линии распила. Если же все-таки распил вышел неровным, отшлифовать его можно мелкой наждачной бумагой. Когда все элементы подготовлены и выверены, можно приступать к наклеиванию. Для этого рекомендуется использовать специальный клей, предназначенный именно для полиуретана — неподходящий клей может повредить его поверхность. Приклеивать элементы лепнины из полиуретана следует в следующем порядке:
- клей густым слоем наносится на поверхность элемента;
- смазанный клеем элемент плотно прижимается к поверхности стены или потолка (лучше и к той, и к другой) таким образом, чтобы избыток клея выдавился наружу;
- если остаются непроклееные участки, то нужно заполнить их клеем;
- лишний клей, выдавленный наружу, после засыхания срезать острым лезвием и зачистить место среза мелкой наждачной бумагой.
На этом приклеивания лепнины из полиуретана завершено. Как видно, все выполняется достаточно просто и быстро и даже без посторонней помощи. А свой внешний вид лепнина из полиуретана сохранит на долгие годы. Именно из-за совокупности этих факторов полиуретановый декор практически вытеснил с рынка изделия из гипса, металла и прочих не самых удобных в использовании материалов.
cassuspro.ru
Производство форм из полиуретана своими руками
Формы из полиуретана своими руками
Как самому сделать матрицу для производства форм из полиуретана или силикона
В строительстве часто используют формы, чтобы производить различные изделия и продукцию. Самые основные из них — это полиуретановые и силиконовые. В них возможно заливать не только гипс и бетон, их также используют для изготовления ненатурального камня. Все это можно изготавливать своими руками. Даже если кажется, что нужно владеть какими-то знаниями, это ошибочное представление. Данная статья подробно расскажет, как изготовить полиуретановую форму, форму для заливки из гипса, силикона, форму для заливки гипса, бетона. Также научит мастерить своими руками матрицу для производства форм из силикона или полиуретана. Самое основное, это уяснить, как соорудить, согласно правилам, практичный образец для матрицы, которая подойдет для таких материалов, как полиуретан, формопласт и силикон.
Создание искусственного декоративного камня из гипса или бетона с использованием полиуретановых форм
Ненатуральный камень, в нынешнее время, представляет собой неплохой, прибыльный бизнес. Для открытия своего собственного дела, с перспективой дальнейшего роста, не требуется много денежных вложений. Ненатуральный камень можно легко и по всем технологиям сделать своими руками. Но, для начала важно располагать помещением с подходящей температурой, чтобы работы можно было проводить круглогодично. Производство ненатурального камня требует хороших, качественных форм, которые невозможно получить без матрицы. К изготовлению образца матрицы нужно подойти очень ответственно, ведь от этого зависит прочность конечного продукта.
Изготовление форм в домашних условиях
Некоторый считают невозможным процесс изготовления в домашних условиях искусственного декоративного камня. Но, благодаря стремлению и желанию все становится возможным. Материалы лучше иметь хорошего качества и сочетать с некоторыми добавками. Например, время схватывания силикона и его текучесть можно отрегулировать, используя катализаторы.
Этап 1. Изготовление образца для производства матрицы, для литья форм
Выпустить матрицу для производства силиконовых и полиуретановых форм своими руками, с помощью которой, будет возможен сам процесс отлива, вполне достижимо. Для изготовления матрицы, нужно приобрести или найти образец, по которому будет возможно скопировать или производить формы, идентичные представленной модели. Если дело касается ненатурального камня, то в данных обстоятельствах образец должен быть совершенной геометрической формы, без щелей и возможных деформированных углов. Чаще всего, для производства форм из полиуретана, для создания ненатурального камня или образца для производства форм под камень применяют разнообразное сырье. Например, гипс, гипсокартон или пенопласт. Иногда приходят к методу копирования из ненатурального или гипсового камня, но идеальным вариантом считается образец из натурального камня. Для этого берется природный камень, нарезается тонкими пластинами (примерно 1 см) и склеивается с помощью клея. Камень должен приобрести безупречную во всех отношениях геометрию. Если имеются неровные стороны или выступы, то на помощь придут болгарка и станок, которые выровняют или уберут все ненужные детали. Готовый камень с убранными неровностями готов к наклеиванию.
Этап 2. Производство матрицы для создания форм из полиуретана или силикона, формопласта, жидкого пластика
Созданную модель нужно наклеить на какую-нибудь основу, чтобы изготовить с нее матрицу. Отличным вариантом будет использование ДСП в качестве подставки. Готовую модель необходимо приклеить к ДСП с помощью силиконового герметика. Но делать это можно исключительно на глянцевой стороне подставки.
Для склеивания берется силиконовый герметик и наносится на обратную сторону заготовленной модели. Хорошенько проходятся все края и углы. Переворачивая камень, следует плотно прижать его к подносу из ДСП. Далее, шпателем аккуратно пройтись по местам стыка, следя за тем, чтобы все пузырьки воздуха исчезли. Лишний воздух ни к чему при заливке полиуретаном или силиконом. После замазывания, заготовку следует оставить до полного высыхания. После этого, настало время для сооружения бортиков для матрицы. Высота стенок должна превышать высоту наклеенного камня. Материалом для этого могут стать пластиковые, стальные или дюралевые уголки. На расстоянии приблизительно 1,5 см от готовой модели, уголки нужно прикрутить с помощью шурупов к ДСП по всему периметру. Важно, после прикручивания, внимательно пройтись с помощью силиконового герметика по всем стыкам и углам, еще раз перепроверив надежность и герметичность конструкции. Иначе текучий полиуретан или силикон, имеющий способность проникать даже в самые малогабаритные щели, вытечет из матрицы. Чтобы весь материал хорошенько высох, лучше оставить матрицу высохнуть (около 12 часов). Рекомендуется пользоваться силиконовым герметиком для аквариумов. Его главной особенностью является исключение усадок или трещинок, которые часто появляются после высыхания. Матрица, обработанная таким герметиком, прослужит многие годы без проблем.
Убедившись в полном высыхании почти готовой матрицы, следующим этапом будет ее смазывание специализированным разделителем. Такую смесь можно приобрести в любых строительных магазинах. Почти вся она имеет восковою основу, а отличается только производителями. Самым лучшим разделителем считается английский. После нанесения он совершенно высыхает, рассеивается и уже после нескольких часов, в приготовленную матрицу, можно вливать полиуретан, формопласт, гипс или силикон. Подойдут любые составы, применяющиеся для создания форм.
Этап 3. Правило заливания полиуретана в матрицу при изготовлении полиуретановой формы
Во — первых, следует решить с выбором самого вещества. Например, если речь идет о ненатуральном камне, то правильным будет произвести формы с полиуретана. А так, заливать разрешено любым, приспособленным для таких работ, материалом. На больших заводах и предприятиях применяют специализированную аппаратуру, которая облегчает задачу. Но, залить форму можно и своим трудом. Как это правильно делать?
Есть ненатуральные камни с разным количеством углов. Такой камень красиво смотрится и пользуется хорошей популярностью. Для него, полиуретановая форма самый лучший вариант. Она удобна и практична, легко чиститься и не создаст никаких нежелательных погрешностей. Процесс заливки – дело тонкое и тут необходим стол или какой-то другой предмет, который будет стоять четко по уровню. Готовый силикон или полиуретан (как его приготовить производители сами пишут на упаковках материала) нужно вливать медленной струей, исключая попадание и образование пузырьков воздуха. Матрицу, при этом, важно слегка наклонить в одну сторону. Когда раствор достигнет нижней стенки матрицы, всю конструкцию можно опустить, и продолжить заливание материала. Оставленная на сутки, матрица застынет и примет подходящую форму.
Полностью высохнув, матрица готова к разборке. Использовать ее для производства ненатурального камня пока рано. Для лучшего закрепления, продукт желательно оставить в теплом месте на некоторое время. Это нужно для того, чтобы у формы были исключены неровности на стенках или поверхности. Особенно это касается полиуретана, так как этот материал обладает памятью и, если его согнуть и оставить так на короткое время, он останется таким. Простояв в теплом помещении, у таких форм увеличивается срок эксплуатации, независимо от того, каким раствором их будут заливать.
Полиуретан и силикон боятся холода, поэтому самая оптимальная температура воздуха составляет от 25 градусов. Если будет прохладно, материал закристаллизуется и его можно будет только выбросить.
Важно! Если по какой-то причине полиуретан закристаллизуется, хотя срок годности еще хороший, не следует торопиться его утилизировать. Устремив на него теплый поток воздуха, полиуретан способен стать опять пригодным для дальнейшего пользования.
Если производство формы вы делаете собственноручно, тогда не стоит покупать полиуретан, рассчитанный для машинной переработки. Он застывает очень быстро, поэтому внимательно читайте упаковку. Также есть полиуретан, направленный на изготовление лепнины, лепки или прочих архитектурных подделок, а для заливки матриц он не годится.
Бетон AREA
legkoe-delo.ru
Виды жидкого полиуретана для изготовления форм
Полиуретан – удивительный продукт, созданный человеком. Используя его можно отлить форму, с помощью которой потом клонировать различные изделия. Например, с помощью полиуретановых форм изготавливаются матрицы для отливки гипсового и цементного искусственного камня. Так же некоторые виды полиуретанов настолько прочны, что хороши в производстве статуэток из бронзы, пластика, а так же гипса. Если вы хотите своими руками сделать полиуретановую форму, то вам не лишне будет изучить виды жидких двухкомпонентных полиуретанов.
VytaFlex Series — серия полиуретанов (ПУ) нового поколения для изготовления форм и резинотехнических изделий. Данная серия специально разработана для заливки бетона при производстве искусственного камня, стеновых панелей, фасадных элементов, скульптур и т.п. Полиуретаны серии VytaFlex имеют удобное соотношение смешения 1А:1В по весу или объему и доступны с твердостью 10, 20, 30, 40, 60 по Шору А.
Brush-On Series — серия тиксотропных полиуретанов, применяющихся для изготовления оболочковых форм для литья бетона, гипса, восков и т.п. Материалы наносятся кистью или шпателем, в том числе на вертикальные поверхности, имеют удобное соотношение смешения 1А:1 В по объему и доступны с твердостью 40 и 60 по Шору А.
РМС-770, 780, 790 — серия полиуретанов высокой твердости 70, 80 и 90 по Шору А, которые показывают высокую прочность и устойчивость к истиранию. РМС-770, 780, 790 имеют соотношение смешения компонентов 2А:1В по весу, низкую вязкость и полимеризуются при комнатной температуре. Данные ПУ используются по всему миру для литья агрессивных материалов, таких как бетон, а также для создания резиновых механических деталей различной конфигурации, например, для производства втулок для шаровых мельниц и отбойных подушек.
Smooth-Cast 300 Series – жидкие полиуретановые пластики снежно-белого цвета, которые обладают очень низкой вязкостью, легко окрашиваются в массе и смешиваются в соотношении 1А:1В по объему. Изделия из полиуретанов серии Smooth-Cast 300 обладают высокой прочностью, износоустойчивостью, легко поддаются механической обработке и поверхностному окрашиванию. Данный продукт обладает высокой влагостойкостью и устойчивостью к воздействию слабых растворителей. Сфера применения пластиков серии Smooth-Cast 300 включает в себя изготовление и репродукцию маленьких и среднего размера скульптур, имитаций изделий из бронзы, серебра и др. металлов, изготовление прототипов моделей для различных отраслей промышленности, декоративной бижутерии и пр.
Smooth-Cast ColorMatch 325 Series — быстроотверждающиеся полиуретановые пластики с низкой вязкостью и удобным соотношением смешения компонентов 1А:1В по объему. Продукты серии ColorMatch нейтральны по цвету и специально разработаны для достижения точного воспроизведения в отливках желаемых цветов с необходимой степенью насыщенности при введении красителей или пигментов (So-Strong или Ignite). Smooth-Cast 325, 326, 327 также прекрасно подходят для ввода наполнителей (URE- FIL 3,5) для создания эффекта “мрамора” или “дерева” в отливках. Smooth-Cast 325 точно копирует внешний вид металла при добавлении бронзовой, медной или иных металлических пудр (Metal Powders).
Smooth-Cast ONYX fast, slow — не содержащая ртуть жидкая пластмасса, которая быстро отверждается при комнатной температуре в твердый пластик глубокого черного цвета. Имеет максимальную твердость 80 по Шору D и обладает повышенными физико-механическими свойствами и температуростойкостью по сравнению с обычными пластиками.
Smooth-Cast 385 — полиуретановая смола с минеральным наполнителем, обладающая повышенной твердостью и прочностью. Smooth-Cast 385 отверждается при комнатной температуре практически без усадки и отливка обладает твердостью 85 по Шору D. Smooth-Cast 385 используется для создания промышленных деталей, для вакуумного формования отливок и в некоторых случаях для изготовления изделий, имитирующих керамику.
Crystal Clear Series — это двухкомпонентные алифатические полиуретаны оптической прозрачности, обладающие стойкостью к воздействию ультрафиолета, используемые как для промышленного (линзы, корпуса приборов и т.п.), так и декоративного применения. Яркие цвета в массе материала достигаются путем добавления специальных красящих пигментов. Для этого материала требуется дегазация.
Task Series — жидкие ПУ пластики технического назначения. После полимеризации пластмассы данной серии показывают превосходную сопротивляемость растяжению и изгибу. TASK 2 и 3 обладают высокой прочностью и низкой вязкостью. TASK 8 имеет теплостойкость до +130 С°. Серия TASK специально разработана для разнообразных индустриальных применений, изготовления тонкостенных высокопрочных изделий, а также крупногабаритных изделий методом холодного ротационного формования (TASK 15). Серия TASK допускает изготовление объектов с толщиной стенок до 1,27 см.
Task 7 FlameOut — новый быстроотверждающийся заливочный пластик с низкой вязкостью, отвечающий требованиям огнестойкости UL 94 V-О. Он не содержит ртуть, TDI или MOCA. Task 7 FlameOut используется для изготовления огнеупорных прототипов и архитектурных элементов, моделей игрушек, тематических элементов для парков и сцены, долговечных макетов и приспособлений для спецэффектов. Также материал может быть использован в целях герметизации и капсулирования.
Plasti-Paste — двухкомпонентный полиуретан, предназначенный для изготовления жестких корковых оболочек. Компонент А — жидкий, компонент В — очень вязкая, нетекучая паста. Соотношение компонентов по объему 1А:ЗВ или по весу 41А:100В, время жизни смеси 8-10 минут (в зависимости от массы). Plasti-Paste хорошо наносится и удерживается на вертикальных поверхностях без образования подтеков. Plasti-Paste наносится на поверхность шпателем и не имеет запаха. После полимеризации Plasti-Paste обладает высокой прочностью, стабильностью и малым весом. При необходимости может быть механически обработан.
Серия двухкомпонентных пенополиуретанов FOAM-iT! (твердый ППу различной плотности) и FlexFoam-iT! (эластичный ППу различной плотности) — просты и удобны в использовании, не требуют специального оборудования для смешения и нанесения, быстро отверждаются и готовы к использованию. Применяются для изготовления различных легких изделий, а также кожухов к тонким оболочковым формам из полиуретана или силикона.
kobzewa.ru
Стоит ли пытаться сделать ППУ самостоятельно? Все о производстве пенополиуретана.
Многие строители понимают важность высококачественной теплоизоляции, но вынуждены экономить на материалах и работах по монтажу. Из-за этого нередко возникает вопрос, как самому сделать пенополиуретан и с его помощью реализовать качественное утепление дома. Прежде, чем заняться воплощением этой идеи, мы советуем разобраться в тонкостях процесса производства ППУ.
Как делается пенополиуретан: базовый принцип
Производство ППУ подразумевает очень сложный технологический процесс. ППУ масса формируется вследствие реакции между полиолом и диизоционатом или полимерным изоционатом в присутствии определенных катализаторов и прочих добавок. Так как производить сам пенополиуретан приходится непосредственно перед заливкой или напылением, завод-изготовитель поставляет две фазы ППУ-смеси в отдельных контейнерах. Фазы смешиваются в специальных установках перед выполнением работ. Вот что происходит при смешивании двух фаз:
Из-за многообразия изоцианатов и огромного спектра полиолов можно получить полиуретаны с различными свойствами и сферами применения. Это может быть эластичная пена, жесткая пена, эластомер и т.д. Узнать все о производстве пенополиуретана невозможно, так как точная рецептура фаз держится производителями в секрете. Даже при наличии всех необходимых компонентов опытному химику придется долго подбирать нужные пропорции для обеспечения требуемых свойств смеси.
Трудности при самостоятельном изготовлении ППУ
Обычно строители закупают готовые фазы для производства пенополиуретана, так как сделать ППУ смесь своими руками можно только из готовых компонентов. Для этого необходимо правильно рассчитать расход и пропорцию фаз ППУ , учитывая все влияющие на это факторы.
Совет от профессионалаДля правильного расчета расхода и достижения максимального эффекта от теплоизоляции важно выбрать смесь ППУ подходящей плотности. В зависимости от нее, теплоизоляция также может выполнять функции влагозащиты, изоляции звука, обладать достаточной прочностью для различных механических воздействий. Все эти особенности в большой степени зависят от плотности ППУ, и вы можете выбрать марку в соответствии с необходимыми качествами материала.
Если вы решили нанести слой теплоизоляции своими силами, вам понадобится изучить, как самостоятельно сделать пенополиуретан установку. В идеале это должен быть аппарат высокого давления, который равномерно смешивает обе фазы ППУ в одну массу и под высоким давлением распыляет полученную смесь по поверхности в виде мелкодисперсной пены. Здесь требуются специальные знания, так как сделать установку для замешивания пенополиуретана необходимо с соблюдением всех технологических требований. В домашних условиях нет возможности проверить качество получаемой ППУ-пены. Химикаты могут смешиваться неравномерно и реагировать друг с другом не до конца, что может привести к опасным испарениям в процессе эксплуатации теплоизоляции. Ознакомьтесь с условиями достижения полной безопасности ППУ. Так как сделать пенополиуретановую установку самому с обеспечением регулируемого давления, температуры и прочих параметров очень сложно, чаще всего строители покупают уже готовые пеногенераторы.
При самостоятельном производстве ППУ из готовых компонентов есть три главные проблемы:
- Неправильный расчет пропорций фаз в смеси
- Неравномерное смешивание фаз ППУ, что приводит к утрате теплоизоляционных свойств и возникновению риска для здоровья
- Отсутствие необходимых навыков для напыления слоя ППУ требуемой толщины, что грозит серьезным перерасходом материалов.
Избежать подобных рисков можно только используя готовое специализированное оборудование и обладая необходимыми навыками в работе с пенополиуретаном. Профессионалы обучаются, как сделать смесь из пенополиуретана и применять ее для теплоизоляции минимум 6 месяцев. В результате специалист знает все тонкости настройки распылителей, умеет производить напыление и заливку ППУ равномерно, с минимальным расходом материалов, исключая все возможные риски для здоровья. Так как сделать и распылить пенополиуретан своими руками, можно только при серьезных финансовых и временных затратах, платные услуги профессионала по факту могут обойтись гораздо дешевле.
moteplo.ru