Из чего делают деревянный брус?
Количество построенных домов из бруса на территории всей нашей страны ежегодно растёт. Этот материал является натуральным, тёплым и практичным. В данной статье мы подробно расскажем о том, какие породы деревьев используются для производства строительного бруса.
Данное дерево довольно часто используется для производства бруса. Особенностью этого материала является высокая плотность и большое содержание смолы.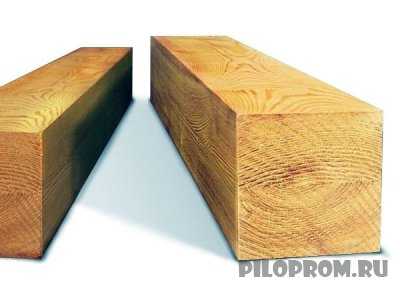
Брус из сосны достаточно тяжёлый, особенно если речь идёт о дереве, которое не сушили после обработки. Жилые дома для постоянного проживания из соснового бруса желательно утеплять.Данная порода дерева наиболее часто используется для производства строительного бруса. Ель достаточно тёплый материал, который имеет небольшой удельный вес.
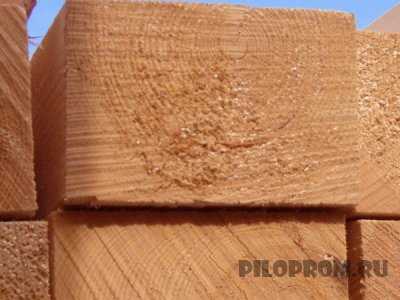
Еловый брус можно использовать для постройки бани, при этом даже в парилке из него не будет выделяться столько смолы, сколько выделяет брус из сосны.
Осина
Осина не так часто используется для производства бруса. Это связано с некоторыми особенностями материала. В частности, осина долго сохнет, а после высыхания значительную часть материала коробит.
Это ведёт к большому проценту брака. Получить качественный брус из осины можно только в том случае, если строго соблюдать технологию производства. Однако данная порода дерева достаточно долговечна и устойчива к воздействию вредителей.
Липа
Брус из липы для строительства наружных стен применяется достаточно редко. В основном данный материал используется для внутренней отделки. Особенно это актуально, когда речь идёт о парилке в бане.
Липа почти не нагревается и приятна на ощупь, что делает её незаменимой при обустройстве полов и полков.Это наиболее прочный материал, который повсеместно применяет для производства бруса. Брус из лиственницы можно применять для строительства несущих стен дома.

Срок службы этого материала составляет не менее 70 лет, а при правильной эксплуатации и более 100 лет. Брус из лиственницы очень плотный, поэтому стены из него нужно утеплять.Дубовый брус очень прочен, но его применение весьма ограничено его ценой. Кроме того, он имеет большую массу, и монтаж дубового бруса существенно осложнён.

По этой причине данный материал используется только в нагруженных конструкциях или для первых венцов дома.
Пользуясь данной информацией, можно выбрать материал для строительства, который идеально подойдёт для сооружения необходимого строения.
Выбирайте строительный деревянный брус в разделе бурс нашего сайта. Там же вы найдете полное описание пиломатериала и цены на все типоразмеры брус.
piloprom.ru
Технология производства клееного бруса. Из чего делают клееный брус
Строительный многослойный материал изготавливают из предварительно подготовленного массива древесины. В качестве сырья используются обрезные доски, изготовленные из деревьев хвойных пород.
Современная технология производства клееного бруса включает подготовку, изготовление и обработку готового материала.
Этапы производства
На начальном этапе происходит подготовка древесины. Бревна распускают на доски в соответствии с необходимыми размерами и помещают в сушильные камеры. Сушка происходит до установления уровня влажности древесины в 10 %.
Отклонение, которое допускается в сторону повышения параметра или понижения не превышает 2%. После сушки строительный материал отправляется в цех для проверки качества материала. Специалист при помощи влагомера проверяет уровень влажности.
Проверка
Если полученные значения не соответствуют допустимым параметрам, то заготовки возвращаются в подготовительный цех. В зависимости от того превышен показатель влажности или понижен, доски отправляются на досушку либо кондиционирование соответственно.
Материал, который прошел контроль влажности, проверяется на наличие дефектов. Все обнаруженные недостатки устраняются и доски сшиваются в мини-шип. На этой стадии процесса производства клееного бруса получаются ламели, которые являются основным сырьем. Далее, ламели и доски строгают.
Склеивание
На следующем этапе в производство включаются клееналивочные станки. С их помощью на высушенные, проверенные и оструганные ламели и доски наносят клей. Количество склеиваемых ламелей варьируется от 2 до 6 штук. В зависимости от типа получаемого изделия ширина и высота могут быть разными.
Для непрофилированного бруса допускается ширина до 1,3 м, а высота определяется размером доски. Для получения профилированного изделия, используется ширина в 240 мм и высота в 180 мм. Клей, который применяют для производства клееного профилированного бруса, выбирается исходя из жестких требований безопасности.
Материал должен быть экологически безвредным, в составе не содержать формальдегида, тяжелых металлов, токсичных веществ, толуола и других, опасных для здоровья человека или окружающей среды компонентов. Клей проходит сертификацию и должен соответствовать специальному стандарту, который разрешает использовать его в производстве продукции, контактирующей с едой.
На некоторых предприятиях применяется безопасный полимерный клей, изготовленный на основе изоционатной эмульсии. На клееналивочных станках на поверхность материала наносится клей в виде тонких непрерывающихся линий. Такой способ нанесения исключает появление потеков на кромки заготовки в момент запрессовки. Доски и ламели собираются в пакет и по транспортному оборудованию направляются в цех для прессовки.
Под действием горизонтального механического пресса создается высокое давление на заготовки. В таком состоянии они выдерживаются до полного высыхания клея. На этом этапе стало понятно, как делают клееный брус, материал осталось только тщательно обработать.
Механическая обработка
После склеивания заготовки отправляются в цех механической обработки, где мастера придают изделиям товарный вид.
На этом этапе используется разное деревообрабатывающее оборудование. В зависимости от конструкционной необходимости нарезают чаши, выполняют профилирование, торцовку на специальном станке, строжку по ширине.
Защита
Технологический процесс производства бруса завершает обработка антисептиком и специальным составом для повышения огнестойкости. Работа выполняется сотрудниками вручную. На поверхность изделий состав наносится при помощи малярной кисти. Для получения высоких показателей прочности и влагостойкости клееный брус после химической обработки выдерживается в течение суток. Как и из чего делают клееный брус, разобрались.
На предприятиях по этой технологии изготавливается два вида бруса: ограждающий и несущий. Несущий строительный материал используется в качестве перекрытий, стропил, колонн. При изготовлении, изделия усиливают арматурой из металла или пластмассы. Она вклеивается в середину бруса. Для производства ограждающих конструкций армирование не используется.
По сравнению с круглым бревном, клееный брус имеет лучшие теплоизоляционные показатели, позволяет получать хорошую плотность прилегания, обеспечивая конструкции высокую воздухонепроницаемость.
Благодаря профилированным пазам и гребням изделия жестко фиксируются в рядах. Конструкция из клееного бруса выглядит монолитной и не требует отделки. Постройка практически не дает усадку и со временем не меняет первоначальной формы. Этот материал приобрел большую популярность в малоэтажном строительстве.
Loading … Спасибо Вам за добавление этой статьи в: rmnt.netМожно ли сделать качественный профилированный брус своими руками
Добротный деревянный дом для многих является идеальным воплощением их мечты об уютном и экологически чистом жилье. В настоящее время оптимальным строительным материалом для такого дома является профилированный брус, который позволяет возводить абсолютно ровные и красивые стены, не нуждающиеся в дополнительной декоративной отделке.
Однако, из-за достаточно высокой стоимости этого материала не все могут себе это позволить, поэтому многие пытаются решить эту проблему по другому – например, сделать профилированный брус своими руками.
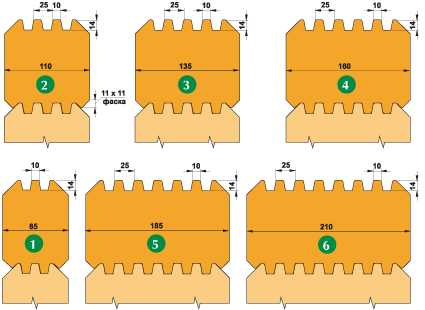
Фото промышленных образцов с заданными размерами
Прежде чем рассматривать различные варианты и способы самостоятельного изготовления, будет не лишним узнать, какие преимущества это может дать и насколько это выгодно.
Когда самостоятельное производство будет оправданно
В зависимости от ситуации у каждого застройщика будет своя мотивация к действию:
- В первую очередь – это финансовый вопрос. Действительно в ряде случаев можно существенно сэкономить, однако здесь нужно еще учитывать временной фактор;
- Довольно часто возникает необходимость в нестандартных размерах бруса, которые невозможно найти у производителей и тогда это практически единственный выход из ситуации;
- Когда уже имеется достаточный запас обрезной доски и бруса, но продать его невыгодно, а для строительства нужен именно профилированный материал;
- Если существует потребность в мощных несущих балках и в данном случае можно изготовить клееный брус своими руками из толстых досок. Такая конструкция не подвержена кручению и растрескиванию, а также выдерживает более высокие нагрузки, чем аналогичная балка из массива дерева.

Варианты нестандартных балок
Для такого решения могут быть и иные причины, но в любом случае нужно заранее просчитать, насколько это выполнимо и оправдано в конкретной ситуации.
Описание способов самостоятельного изготовления профилированного бруса
В зависимости от опыта и технической оснащенности домашней мастерской, можно выделить несколько вариантов по уровню их сложности.
Изготовление бруса из досок
Если в наличии нет практически никакого деревообрабатывающего оборудования, то самым простым выходом будет изготовить брус из досок.
Для этих целей наилучшим образом подходит доска «пятидесятка», имеющая подходящие размеры по длине и ширине.
- В первую очередь нужно соорудить из подручных материалов стапель, на котором и будут выполняться все работы;
- Затем изготавливаются специальные шаблоны, по которым будут укладываться доски, чтобы не измерять каждый раз размеры шипа и паза будущего бруса и чтобы все изделия были одинаковые;
- Для производства одного бруса понадобится три доски, которые укладываются друг на друга в длину, причем средняя доска укладывается с заданным по шаблону смещением. В результате такого наложения досок в поперечном сечении образуется профиль, где с одной стороны формируется шип, а с противоположной стороны паз;
- После того как доски уложены надлежащим образом, остается их только надежно скрепить между собой. Самое простое – это сколотить их с двух сторон обычными гвоздями, для более надежного соединения можно использовать металлические саморезы, но в данном случае без шуруповерта не обойтись;
- Также для придания прочности можно склеить брус своими руками, для чего прежде чем укладывать доски друг на друга их тщательно промазывают клеем. В любом случае после этого их необходимо скреплять гвоздями или саморезами, так как в домашних условиях добиться идеально прочного склеивания таких поверхностей очень сложно. В результате получится упрощенный вариант клееного бруса.

Два варианта самостоятельного изготовления
Простой способ доработки прямоугольного бруса
В данном случае профилирование бруса своими руками требует наличия как минимум ручной циркулярной пилы, но в остальном оно не вызовет затруднений даже у начинающего столяра.
- Здесь также понадобится сооружение устойчивого стапеля или верстака на всю длину обрабатываемой заготовки;
- В этом случае основной целью будет вырезать одинаковые V-образные пазы с противоположных сторон прямоугольной заготовки;
- Для точной разметки будущих пазов необходимо изготовить из бруска шаблон с шириной будущего паза, который будет устанавливаться по всей длине бруса ровно по центру. По шаблону отбиваются две параллельных линии, по которым будут выполнены разрезы;
- По контрольным линиям, с помощью ручной циркулярной пилы, выставленной под углом в 45⁰,выполняется надрез по всей длине с противоположных сторон на заданную глубину. В результате должен получиться ровный V-образный паз.

Циркулярная пила для работы
- Теперь если положить два бруса друг на друга сторонами, где пропилены пазы, то по всей длине образуется ромбовидная полость квадратного сечения, в которую следует уложить стандартный брусок 50×50, под размеры которого и необходимо делать пазы.
В результате таких простых действий можно очень быстро превратить прямоугольную деревянную заготовку в профилированный брус. Это два наиболее простых и доступных каждому способа изготовления.
Но в любом случае, прежде чем что-то делать, будет не лишним ознакомиться с Гост 9330 -76, который называется «Основные соединения деталей из древесины и древесных материалов». В этом документе содержатся все необходимые сведения для того чтобы правильно рассчитать профиль в зависимости от размеров заготовки.
Нарезка профиля с помощью ручного фрезера
В данном случае в качестве заготовки будет выступать четырехкантный обрезной брус прямоугольной формы, а основным рабочим инструментом будет мощный ручной фрезер.
Кстати, следует опять же просчитать насколько это рентабельно, ведь цена хорошего инструмента тоже не может быть маленькой, а используя маломощный и дешевый, вы вряд ли добьетесь нужного качества обработки, да и временные затраты будут гораздо выше.

Ручной фрезер для обработки и нарезки профиля
Пошаговая инструкция в данном случае будет выглядеть следующим образом:
- Сооружаем прочную основу в виде стапеля или верстака на всю длину обрабатываемых заготовок. Опора должна быть устойчивой без люфтов и шатаний, а также позволять прочно закреплять заготовку;
- Кроме самого фрезера понадобится еще и набор специальных фрезерных насадок, форма и размер которых будет зависеть от сложности профиля, который необходимо выбрать. При надлежащем опыте и качественном материале можно получить изделия максимально приближенные к промышленным образцам;
- При работе фрезером важно соблюдать точность ведения инструмента по намеченной траектории. Желательно чтобы он плавно двигался по стабильно установленным направляющим, без рывков и боковых люфтов. От точности работы зависит качество сопряжения элементов, а соответственно и такие эксплуатационные параметры будущего дома как теплоизоляция и ветрозащита;
Важно!
Если использовать высоко оборотистый фрезер с острыми фрезами, то можно обойтись без дополнительного шлифования.
Использование такой технологии позволяет в бытовых условиях нарезать на брусе профиль различной сложности, ни в чем не уступающий промышленным образцам. Существуют и другие способы профилирования, но они требуют наличия более сложной самостоятельно изготовленной технической оснастки и оборудования.

Небольшой станок для профилирования деревянных заготовок
В дальнейшем, независимо от того какой тип бруса будет использован для строительства, важно соблюдение технологии, которая предписывает использовать шканты (нагеля) для надежного соединения венцов между собой.
Изготовление шкантов
Данный вид крепежа представляет собой деревянные цилиндрические элементы определенного диаметра, которые забиваются в заранее просверленные отверстия в лежащих друг на друге брусьях, дополнительно скрепляя их таким образом между собой.
Изготовить шканты для бруса своими руками достаточно не сложно и с этим может справиться любой, однако в любом деле есть свои тонкости, которые необходимо знать.
- Шканты по технологии должны изготавливаться из более твердых пород древесины;
- Их диаметр должен быть таким, чтобы они с легким натягом забивались в технологические отверстия. Если крепеж болтается в отверстии, то он практически бесполезен, а если он сидит слишком туго или выступает над поверхностью, то это может вызвать проблемы при усадке дома.

Правильно забитый шкант
Есть несколько простых вариантов изготовления:
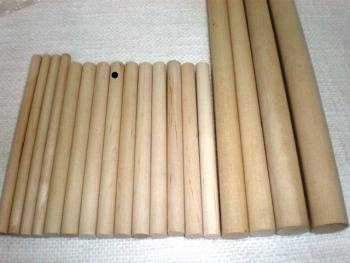
Готовые нагели из березы
- Можно расколоть березовые чурки необходимой длины на множество квадратных заготовок, а затем вручную обтесать их до круглой формы нужного диаметра;
- Если в наличии есть токарный станок по дереву, то эти элементы можно быстро выточить;
- В качестве шкантов можно использовать ставшие непригодными черенки для лопат и другого садового инструмента. В данном случае нужно лишь порезать их на заготовки нужной длины.
Совет!
Также в качестве шкантов можно использовать металлические обрезки трубы подходящего диаметра.
Имитация как вариант декоративной отделки
Довольно часто для создания определенного стиля или внутренней атмосферы в интерьере дома используется имитация бруса своими руками. Такой подход позволяет добиться практически полной визуальной аналогии с настоящим брусом и обладает целым рядом преимуществ:

Внешняя отделка под имитацию бруса
- Имитация может быть выполнена на поверхности из любого материала;
- Значительно сокращается расход древесины, а соответственно финансовые затраты и время на реализацию;
- Такая отделка может быть выполнена после постройки дома в любое время, причем как изнутри, так и снаружи.
Изготовить набор декоративных элементов для такой имитации достаточно несложно и в домашних условиях. Для этого понадобится рассчитанный заранее объем доски толщиной не менее 50 мм, а также электрический рубанок и шлифмашинка.
Процесс изготовления будет заключаться в следующем:
- С помощью рубанка необходимо плавно закруглить края одной из боковых сторон доски, придав ей формы закругления, которые имеет брус;
- Затем с помощью шлифмашинки следует все тщательно зашлифовать, убрав все огрехи и следы от рубанка.

Имитация закруглений
Обработанная таким образом доска очень правдоподобно может имитировать не только брус, го и потолочные балки. Чтобы добиться полного сходства, в углах где сходятся плоскости стен, доски необходимо сместить друг относительно друга на половину их ширины, выполнив имитацию рубки угла сруба.
При желании такой «брус» можно затонировать под ценные породы древесины, еще более усилив эффект имитации.
Заключение
По итогам изложенной в статье информации можно сделать вывод, что брус очень широко используется практически во всех архитектурных проектах частных загородных домов из любого материала. При желании и должном терпении его можно изготовить самостоятельно, используя описанные выше рекомендации.
Дополнительную информацию по данной теме вы также можете посмотреть в видео в этой статье.
Понравилась статья? Подписывайтесь на наш канал Яндекс.Дзен Добавить в избранное Версия для печати1brus.ru
Как производят клеенный брус для деревянных домов
Вопрос о собственной жилплощади возникает рано или поздно у каждого человека. Волнует эта проблема и меня в том числе. Недавно, побывав на одной выставке посвященной строительству дома я заинтересовался вопросом, из чего и как делаются стройматериалы для простого деревянного домика, который по цене доступнее, чем самая дешевая однушка в столице. Я договорился с заводом Good Wood об экскурсии на производство, и на днях выяснил как это делается.Сегодня в специальном репортаже для kak_eto_sdelano мы посмотрим как производят брус из которого строят современные деревянные дома.
Все начинается с того, что на завод поступают вот такие пакеты с деревянными досками. Специалист производства перед началом производственного цикла проверяет каждый такой пакет на соответствие качеству. Выборочно проверяются доски и после подтверждения качества они отправляются на первый этап. Если процент дефектов и сучковин на заготовках превышают допустимые нормы, то такой пакет отправляется обратно поставщику.
Сырье, из которого будет сделан брус — из сосны и ели.
Территория завода не маленькая, вдалеке можно видеть строящийся корпус, в котором будет производится больше заготовок чем в остальных цехах.
После того, как доски выбраны, они собираются в сушильный пакет — набор из заготовок, который будет помещен в сушильную камеру. Доски предварительно перетягивают такой лентой, чтобы в процессе сушки они не деформировались.
На производстве 6 сушильных камер объемом до 75 куб.м.
Заглянем внутрь.
Пакеты с досками находятся в камере 6-8 дней, при температуре 65-68 градусов. Сушильная камера снабжена датчиками влажности воздуха, температуры, чтобы следить за правильной технологией сушки досок.
Это фото свежесклеенного не обработанного бруса, здесь можно видеть, как из досок разного размера делают единый прочный брус. О нем я расскажу далее.
Но вернемся к производству. После сушки пакет с досками попадает в цех.
Здесь он проходит через станок, который строгает доску со всех четырех сторон. На этом этапе рабочие проводят визуальный контроль, каждая доска заново проверяется на наличие дефектов и сучковин. Тут же определяется какие доски пойдут на внутреннюю и внешнюю сторону будущего бруса. Более красивые доски, с меньшим количеством сучковин идут на внешнюю сторону.
Как я говорил, доски из которых делается брус из сосны и ели. Так как они схожи по структуре волокон, их можно без особых проблем склеивать друг с другом. И еще информация для наблюдательных — доски ели и сосны можно отличить по сучковинам — у сосны они крупнее, чем у ели.
Далее, доски склеивают. Здесь аппарат был отключен потому можно на фото из соседнего цеха увидеть склеивающий аппарат в работе.
Вот таким дождем клей покрывает доску с одно стороны.
Лишнее убирается валком. В зависимости от каждого индивидуального заказа брус делают/склеивают из нескольких досок различной длины и ширины. Чуть не забыл сказать — на производстве не делают впрок брус. Его изготовление начинается только после того, как клиент заказал дом (уже подготовил фундамент) или отдельные детали.
Клей используемый в производстве прошел сертификацию на безопасность и не содержит формальдегидов и опасных для человека веществ.
В этой бочке отвердитель, который смешивается с клеем непосредственно перед склейкой.
После того, как доски смазаны клеем и правильно уложены, они помещаются под пресс, в котором находятся 40 минут. Затем их вынимают и они «отдыхают» еще два часа до того, как попадут на следующий этап.
Далее заготовки передвигаются на следующий этап, но перед этим заготовка бруса опять проходит через станок, который обрабатывает его с четырех сторон.
Так выглядит брус после профилирования, но и это еще не все. Как видите торцы неровные, и брусья не нарезаны на нужные детали.
Кстати, точность нарезки профиля определяется такими лазерными датчиками.
Попробовал прожечь свой блокнот, но почему-то не получилось.
Еще одна приятная деталь — кулер с прохладной водой. Очень нужная вещь на производстве.
Но мы отвлеклись. Далее брус попадает на станок, который обрезает торец и…
нарезает чашу — углубление в брусе, необходимое для поперечной сборки. Чаша, кстати, единственное место, которое будет обложено утеплителем. При сборке стен дома утеплитель не используется, только в местах стыка.
Ну, вот и готовы детали для дома. Торцы обрабатываются торцевым герметиком.
А это уже готовый пакет для дома. Таких для одного дома будет несколько.
Каждая деталь маркируется бумажкой со штрих-кодом, в котором содержится вся информация о брусе, вплоть до того, где он должен быть уложен в доме.
И еще одна деталь: после подготовки каждой такой партии для отдельного проекта, делаются контрольные срезы, которые потом исследуются в заводской лаборатории на соответствие качеству. Срез нагревается и охлаждается до определенной температуры в течении 50 циклов, которые имитируют зиму и лето, то есть теоретически дом из такого бруса может простоять 50 лет.
За процессом следит и камера, которая, как мне сказали показывает процесс производства онлайн посетителям сайта завода.
На мониторах отображаются детали производственного процесса. На фотографиях — проекты, которые осуществляются в данный момент.
На примере этого образца, который стоит в цеху можно видеть как выглядит угол стен дома. Такими железными штырями скрепляются только углы, а по остальной длине стен брусы насаживаются на деревянные штыри.
Идем на следующий этап. Здесь готовый брус обрабатывается антисептиком для огне-биозащиты. Он предохраняет его от жучков-короедов, плесени, гниения и предотвращает дом от возгорания. Должен уточнить, что действие антисептика конечно не вечно, но он сохраняет свойства бруса на некоторое время, и в случае пожара дом не воспламенится как спичка, потому что при обработке антисептиком из дерева выводится кислород.
При необходимости брус может принять антисептические ванны.
После этого этапа, можно сказать, что процесс производства и подготовки бруса для заказчика завершен. Однако это еще не все.
После обработки антисептиком брус собирают опять в такие пакеты готовые к отправке клиенту.
На каждом пакете информация о заказчике и содержимом. Обратите внимание на слова «мин. венец 20» и «макс. венец 43» — это означает, что в этом пакете есть детали, которые подходят для сборки от 20 «слоя» стен до 43. Это нужно для того, чтобы не вскрывать все пакеты в поисках нужных деталей — все они могут оказаться в одном пакете, до определенного этапа сборки.
Мы увидели практически всю цепочку производства, однако, наша экскурсия не завершена, мы идем в следующий цех, чтобы узнать еще кое-какие детали. Кстати, обратите внимание на этот домик, здесь находится один из офисов компании, в котором работают менеджеры по продажам, специалисты колл-центра, архитекторы и конструкторы. Как понимаете, он полностью сделан на этом производстве и собран работниками компании.
Кстати, о велосипедах на фото — они безвозмездно покупаются компанией любому работнику производства, который готов ездить на нем из дома до работы и обратно). Еще одна интересная информация о компании: работникам производства, которые бросили курить выдается премия в 10 тыс. руб! Правда, если работник не справляется с недостатком никотина и опять начинает курить, его штрафуют на 15 тыс).
Следующий цех производства больше размером, здесь более новые, немецкие станки, здесь делают брус длиной до 12 метров и супербрус, сечение которых больше, чем у тех, которые мы видели ранее.
В этом цеху брус также делают из отдельных досок, которые сращивают с помощью клея в длинную доску.
Участки досок с дефектами и сучковинами, которые могут повредить будущему изделию вырезают. На этом фото — отход производства.
А это готовые доски, из которых будут клеить брус. Здесь происходит вся та же технологическая цепочка, что мы видели ранее, потому не буду повторяться.
Тринадцатиметровый пресс.
После обработки досок, их торцы нарезаются «елочкой» и далее станок при склейке с давлением прижимает доски друг к другу. Этого достаточно, чтобы склеить доску.
Ну а дальше доски склеиваются в брус, обрабатываются, и на этом станке нарезается профиль. И еще добавлю, что брус, склеенный из отдельных досок различного размера прочнее, чем из цельных досок, потому что дерево со временем дает усадку и в нем повышается напряжение между другими склеенными досками, а короткие нарезанные заготовки полностью минимизируют этот эффект. Поперечные балки при строительстве дома тоже делают из такого бруса, в обязательном порядке.
А вот и супербрус. Кстати, клиент, который заказывает брус для своего дома, выбирает размер сечения под свой вкус. Здесь же, компания может помочь ему определиться с проектом, или создать собственный проект с помощью архитектора и инженеров компании Good Wood.
А это суперстанок Хундеггера, который в этот момент нарезает чашу в брусе.
Заметил, что в цехах хорошо работает вентиляция и пыль, которая неизбежна на таком производстве не висит долго в воздухе.
С пылью и мельчайшими опилками также борются и увлажнители воздуха. Хорошая вещь, надо завести себе дома.
Хотя у производства бывают отходы в виде обрезков, можно сказать, что это практически безотходное производство (в экономическом плане), потому что древесина не пригодная для изготовления бруса продается как топливо для камина, и используется для собственных нужд, также как топливо.
Из опилок делают вот такие брикеты для растопки каминов.
В конце экскурсии мне опять встречаются готовые пакеты для сушильной печи.
В эту емкость собираются опилки производства.
Напоследок зайдем в небольшой двухэтажный домик на территории компании, который может осмотреть любой желающий. Выглядит симпатично.
Чуть не забыл сказать, дома для своих клиентов собирают только специалисты компании, начиная от закладки фундамента, до кровельных работ и установки бойлера, и т.п., что очень удобно.
Здесь есть своя котельная, что немаловажно.
Домик сделан из самого простого бруса. Конечно же, после сборки дома нужно его покрасить, чтобы сохранить его свойства. Кстати, приемущество бруса перед обычным бревном в том, что со временем брус дает усадку всего в 1-2% а бревно — 15%! К тому же цельное бревно невозможно подвергнуть сушке без деформации.
Очень просторная, светлая кухня.
Плавно перетекающая в гостиную. В туалет и ванную заглядывать не стал, так как в этот момент ими были заинтересованы потенциальные покупатели, бродившие по дому).
На первом этаже нет жилых комнат, потому что площадь домика совсем небольшая. А на втором этаже их три. Первые две — детские комнаты.
Третья комната — спальня для родителей.
Тут же есть балкончик. Домик хорош, но маловат, буду присматривать себе другой проект.
Теперь и вы знаете, как делается брус для строительства дома. Спасибо всем, кто дочитал до конца.
А всем, кто заинтересовался строительством собственного домика советую посетить сайт компании Good Wood, где очень подробно рассказывается о различных проектах таких домов, и можно подобрать под свой вкус и цену.
Жми на кнопку, чтобы подписаться на «Как это сделано»!
Если у вас есть производство или сервис, о котором вы хотите рассказать нашим читателям, пишите Аслану ([email protected]) и мы сделаем самый лучший репортаж, который увидят не только читатели сообщества, но и сайта Как это сделано
Подписывайтесь также на наши группы в фейсбуке, вконтакте, одноклассниках, в ютюбе и инстаграме, где будут выкладываться самое интересное из сообщества, плюс видео о том, как это сделано, устроено и работает.
Жми на иконку и подписывайся!
— http://kak_eto_sdelano.livejournal.com/
— https://www.facebook.com/kaketosdelano/
— https://www.youtube.com/kaketosdelano
— https://vk.com/kaketosdelano
— https://ok.ru/kaketosdelano
— https://twitter.com/kaketosdelano
— https://www.instagram.com/kaketosdelano/
Официальный сайт — http://ikaketosdelano.ru/
Мой блог — http://aslan.livejournal.com
Инстаграм — https://www.instagram.com/aslanfoto/
Facebook — https://www.facebook.com/aslanfoto/
Вконтакте — https://vk.com/aslanfoto
kak-eto-sdelano.livejournal.com
видео-инструкция по монтажу, особенности горизонтально-клееного материала, используемого клея, перил, дуплексов, особняков, установки проводки, цена, фото
Все фото из статьи
Клееный брус имеет очень широкую сферу использования в строительстве и мебельном производстве благодаря своим высоким эксплуатационным качествам. Примечательно, что его можно изготовить даже в домашних условиях своими руками. Об этом и пойдёт речь далее.
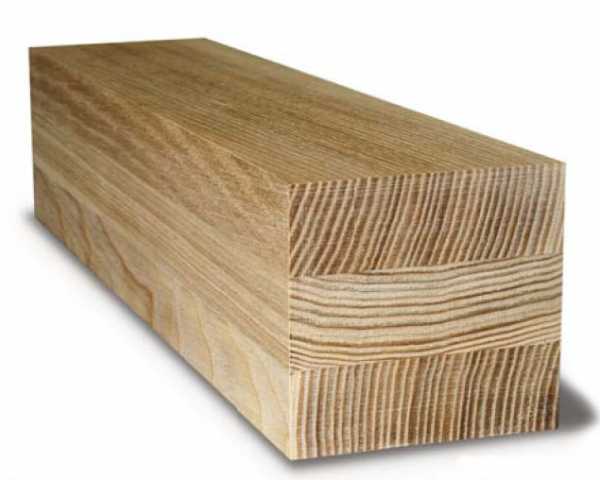
Горизонтально клееный брус – превосходный строительный материал
Общие положения
В первую очередь следует понимать, что собой представляет клееный брус. Это набор тщательно отобранных, подготовленных и склеенных между собой ламелей. Наличие застывших клеевых прослоек значительно меняет технические характеристики изделия в сравнении с цельными образцами. Давайте ознакомимся с основными отличиями.
Преимущества
- Увеличение показателя прочности до DIN 1052, гарантирующее высокую надёжность собранной мебели;

Перила из клееного бруса выдержат колоссальные механические нагрузки
- Снижение теплопроводности, которое наглядно отображает следующая таблица:
Строительный материал | Коэффициент теплопроводности, Вт/(м×К) |
Железобетонные блоки | 2,04 |
Пеноблоки | 0,37 |
Цельный брус | 0,18 |
Клееный брус | 0,1 |
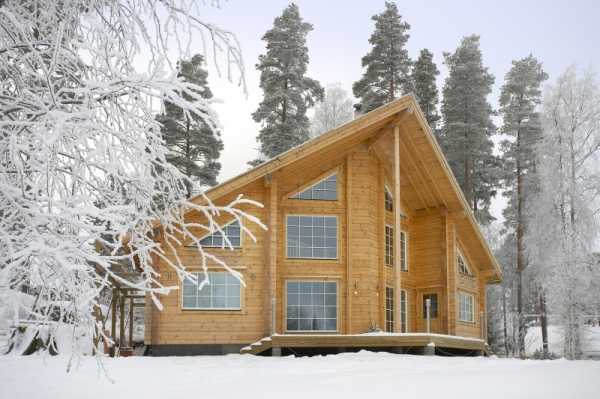
Особняк из клееного бруса не нуждается в дополнительном утеплении
- Уменьшение напряжённости древесины и, как следствие, усадки возведённого здания до практически не ощутимых одного или двух процентов;
- Повышение влагостойкости, исключающее начало процессов гниения и распространения плесени.
То есть, мы видим устранение практически всех возможных недостатков простых цельных деревянных изделий. Но о паре «подводных камней» также стоит знать:
Недостатки
- Относительно высокая цена. Но ведь за качество стоит платить, к тому же вы сэкономите на отсутствии утепляющих материалов, а если ещё сделать клееный брус собственноручно, то повышение стоимости выйдет и вовсе незначительным;
- Возможное понижение экологичности вследствие применения некачественного клея.
Совет: при осуществлении клейки ламелей в домашних условиях очень внимательно отнеситесь к выбору клея соответствующего качества.
Это позволит сохранить необходимый уровень экологической чистоты готового изделия.
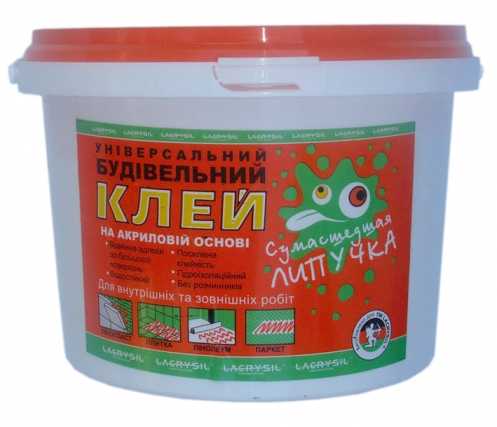
Клей для клееного бруса на акриловой основе
Ход работ
Инструкция, конечно же, начинается с подготовительных этапов.
Этап №1: подготовка необходимого инструмента
Вам понадобятся:
- Ножовка для резки заготовок;
Совет: при наличии возможности рекомендуется использовать электрический лобзик для дерева.
Он значительно упростит и ускорит работу.
- Струбцины. Это чуть ли не самые важные инструменты, которые заменят вам в домашних условиях заводской пресс;

Фото набора струбцин
- Рубанок и шлифовальная машинка для обработки древесной поверхности;
- Кисти для нанесения клея;
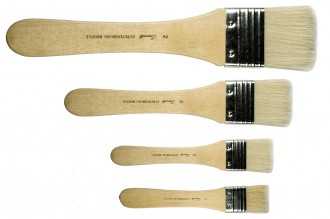
Плоские кисти различных размеров
- Рулетка и другие, необходимые для нанесения разметки, приспособления.

Пример подходящей строительной рулетки
Этап №2: подготовка необходимых материалов
- Древесина в виде досок, цельного бруса или реек, в зависимости от того, в какой области вы планируете использовать готовые изделия;
- Клей, который может быть следующих видов:
Тип клея | Внешний вид | Расход, г/м2 |
Полиуретановый | Жидкость свето-коричневого цвета | 200-450 |
Меламин-карбамид-формальдегидный | Жидкость молочно-белого цвета | 300-450 |
Эмульсионный полимер-изоцианатный | Жидкость молочно-белого цвета | 250-400 |
- Ацетон с целью осуществления обезжиривания склеиваемых поверхностей.
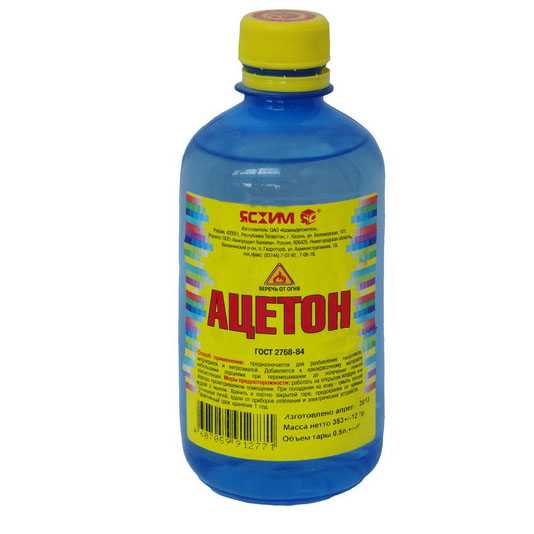
Образец бутылки с ацетоном
Этап №3: создание ламелей
Ламель в данном случае – это одна из склеиваемых частей изделия, соединение которых можно осуществлять одним из следующих методов:

Способы осуществления стыковки ламелей
Обозначение на рисунке | Название метода |
а | На гладкую фугу |
б | В четверть |
в | На шпонку |
Совет: при этом старайтесь, чтобы рисунок годовалых колец был направлен в различные стороны.
Это позволит уменьшить эффект коробления.
Для примера возьмём три бруска сечением 100 на 100 мм и будем осуществлять соединение на шпонку.
Для этого:
- Обрезаем каждый пиломатериал до нужной нам длины;
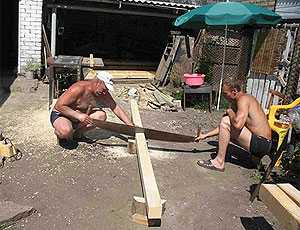
Распилка заготовок
- Строгаем и шлифуем те стороны, которые будут склеиваться;
- Далее у боковых ламелей выбираем паз с одной стороны, а у средней с обеих;

Ламели с выбранными пазами и вставленными ламелями
- Соединяем все элементы на сухую и при необходимости дорабатываем их для более качественной стыковки.

Соединённые элементы
Если вы в дальнейшем планируете применить готовое изделие для монтажа внутренних перегородок в доме, то есть смысл создать дополнительный паз для прокладки проводки.
Проводка в клееном брусе отлично маскируется
Этап №4: предварительная обработка
Чтобы склейка прошла идеально обрабатываем сопрягаемые плоскости:
- Выполняем шлифовку шлифовальной машиной;

Процесс шлифовки
- Устраняем весь собравшийся мусор и древесную пыль с помощью щётки или пылесоса;
- Тщательно обезжириваем ацетоном и оставляем заготовки просохнуть;
- Наносим слой антисептика и снова ждём высыхания деревянных поверхностей;
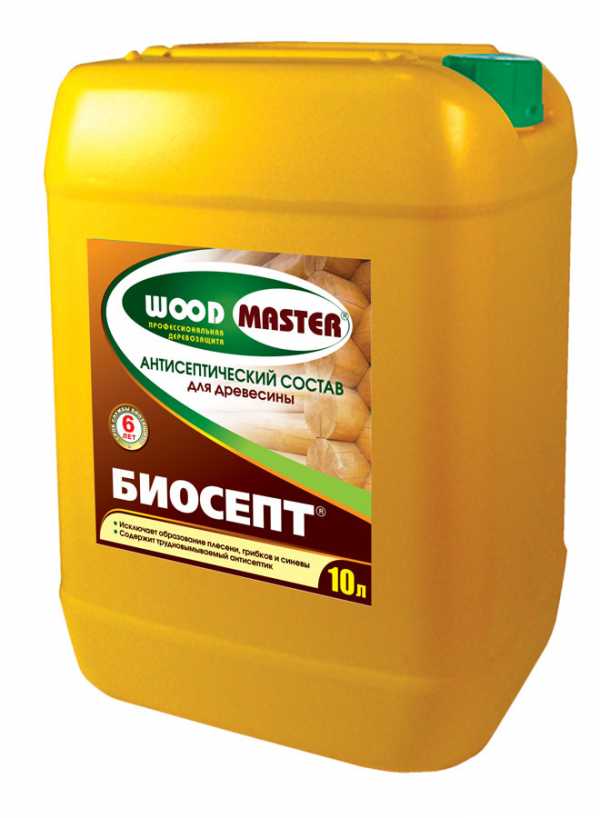
Пример подходящего антисептика

Пример подходящего антипирена
Таким образом, мы получаем гладкие, чистые, защищённые от сырости и возгорания древесные поверхности, готовые к дальнейшим операциям.
Этап №5: склеивание
Теперь переходим к выполнению наиболее важной задачи:
- Разводим клей в соответствии с инструкцией на упаковке в удобной чистой ёмкости;
- Макаем в получившуюся смесь кисть, после чего тщательно обрабатываем ею подготовленные плоскости;
- Вставляем в пазы шпонки и также наносим на них клей;
- Далее соединяем все элементы и крепко стягиваем их струбцинами, после чего оставляем изделия до момента полного застывания клеящего раствора в сухом месте, не подверженном прямому воздействию солнечных лучей.

Промазанные клеем и зажатые струбцинами ламели
Этап №6: окончательная обработка
После того, как изделие полностью высохнет, выполняем финишные операции:
- Строгаем и шлифуем получившийся брус со всех сторон;
- Пропитываем антисептиком и антипиреном;
- После просыхания можем использовать по назначению.
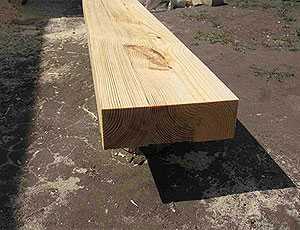
Готовый клееный собственноручно брус
В некоторых случаях для повышения прочности соединения можно использовать специальные шканты, которые вставляются в заранее просверленные отверстия и скрепляют ламели.
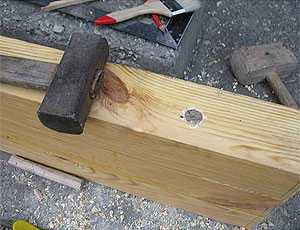
Дополнительная фиксация шкантами
Заключение
Клееный брус очень надёжный, тёплый и простой в эксплуатации строительный материал. Единственный его существенный недостаток – это достаточно высокая стоимость. Но, во-первых, за качество следует платить, во-вторых, можно существенно сэкономить, выполнив склеивание собственными силами. Примечательно, что некоторые технические параметры самодельного изделия при этом могут оказаться даже лучше, чем у заводского.

Готовые дуплексы из клееного бруса
Видео в этой статье сможет ознакомить вас с некоторой дополнительной информацией, имеющей прямое отношение к изложенной выше теме. Пробуйте, и у вас всё выйдет.
Понравилась статья? Подписывайтесь на наш канал Яндекс.Дзенrubankom.com
Как самому сделать клееный брус
Клееный брус представляет собой пиломатериал, состоящий из нескольких склеенных между собой деревянных полотен. Изготовленный самостоятельно, он выгоднее заводского не только в финансовом отношении. Собственноручно сделанный пиломатериал может быть любого размера, сечения, более высокого качества.Относительно последнего параметра от покупателей заводского клееного бруса поступает много нареканий. В целях экономии для склеивания производители нередко используют древесину низкого качества, что определяет невысокие прочностные характеристики готового изделия.
Доски, из которых склеивают брус, называют ламели. Они должны быть ровными, без признаков гнили, трещин, хорошо высушенными, с минимальным количеством сучков. Основное правило склеивания бруса таково: ламели должны быть уложены так, чтобы их годовые кольца были разнонаправлены.
Помимо древесины следует запастись клеем. Оптимально использовать ПУР-Клей 510 FiberBond. Этот состав разработан для склеивания древесины, поэтому обеспечит высокую прочность соединения досок. Но можно взять и любой другой, предназначенный для работ по дереву. Из инструментов понадобятся струбцины, ножовка, растворитель для обезжиривания материала, огнебиозащитный состав, наждачная бумага средней зернистости.
Клееный брус можно изготовить тремя способами: методом соединения трех ламелей; двух ламелей, соединенных буквой Z; склеенный из ламелей со вставками. Наиболее часто используется первый, так как он значительно проще и быстрее.
Сначала производят отбор досок для склеивания бруса, затем укладывают их одна на другую так, чтобы годовые кольца были направлены в противоположные стороны. Затем доски следует подписать простым карандашом или маркером. Эта предосторожность позволит не перепутать очередность их укладки.
Затем, центральную доску с обеих сторон обрабатывают наждачной бумагой, что придаст ей шероховатость. Она повысит адгезию клея к древесине. Боковые ламели обрабатывают только с одной стороны: той, которая будет находиться внутри бруса.
Далее, производится обеспыливание и обезжиривание этих поверхностей с помощью растворителя и огнебиозащитного состава. Эти жидкости поочередно наносят на доски: сначала растворитель на ошкуренные поверхности, а после его высыхания – защитная пропитка. Ею покрывают все стороны пиломатериала, включая торцы.
Затем на ламели наносят клей слоем 1-2 мм. Доски укладывают друг на друга так, чтобы их торцы образовывали единую плоскость с каждой из сторон бруса. После чего ламели скрепляют струбцинами, которые должны отстоять друг от друга на 40-45 см. Время высыхания клея указано в инструкции к составу, но оно обычно не превышает 1-2 дней.
www.kakprosto.ru
Из каких деревьев делают брус?
Существует множество пород деревьев, из которых изготавливают брус. Каждое из них имеет свои преимущества перед остальными. Какое то дешевле, какое то дороже. Какое то полезнее, какое то вреднее. Ниже перечислим не большой список деревьев из которых делают брус.
Рассмотрим основные из них:
Брус из Ели
В основном брус выпиливается именно из ели. Такой брус хорошо использовать для постройки бани и дома в связи с высокими теплоизоляционными свойствами дерева и небольшим весом. Единственный, но существенный недостаток – подверженность гниению.
Брус из Сосны
Является вторым по распространенности деревом. Главное отличие от ели – высокое содержание смолы и наличие сучков. Брус из сосны тяжелее и плотнее, чем из ели. При этом теплопроводность у него выше, а, значит, постройка будет холоднее.
Брус из Осины
Несмотря на свои недостатки осина довольно востребована. Высыхает она долго, а после высыхания большую часть сруба сильно поведет. Но если соблюдать все правила, например, произвести правильную сушку или сбор конструкции, то выбраковки можно избежать. Однако, для этого необходимо иметь огромный опыт работы с осиной и специальные знания. При правильной сушке осина очень долговечна. Подкупают и плюсы такого дерева как материала: небольшая стоимость дерева, практически полное отсутствие гниения и смолы.
Брус из Липы
Для масштабных строек липа не применяется . Причина – быстрое гниение. Но при этом использование липы при постройке бани предпочтительно, хотя сама баня будет не очень долговечна. Не простоит и больше 30 лет. На практике из липовых брусков делают лавки и полки, застилают пол. Несомненные преимущества липы: легкий вес, небольшая теплопроводность (при использовании в парилке она практически не нагревается) и отсутствие смолы. Что касается минусов, то это, как уже указано, большая подверженность гниению из-за низкой плотности и сильная деформация после высыхания.
Брус из Лиственницы
Одним из самых распространенных является лиственница. Брус из нее очень популярен и востребован. Еще в давние времена люди отмечали долговечность лиственницы – бревенчатый сруб из нее прослужит не меньше 80 лет. Кроме того, у лиственницы очень высокая прочность, довольно приемлемая стоимость и доступность. Естественно, существуют и минусы: дом из лиственницы будет холодными из-за высокой теплопроводности. Да и процесс рубки и монтажа очень трудоемкий – играет роль плотность дерева.
Брус из Дуба
Нельзя не учитывать достоинства дуба. Брус из него невероятно долговечен, прочен, почти не подвергается износу. Но за качество нужно платить: явный недостаток материала из дуба высокая цена. Брус из дуба очень тяжелый, поэтому его трудно монтировать.
houseizbrus.ru